The foundation of any strong structure is its concrete footings, with reinforcement (reo) bars acting as the essential framework that ensures strength. These steel reinforcements work together with concrete to form a durable foundation system capable of bearing heavy loads and resisting environmental forces.
Concrete footings are crucial for:
- Distributing building loads evenly into the ground
- Preventing structural settlement
- Maintaining building stability
- Resisting soil movement and pressure
Installing reo bars in these footings requires skill and attention to detail. Common mistakes during installation can result in:
- Weak structure
- Concrete failure
- Expensive repairs
- Safety risks
- Building code violations
The correct positioning and installation of reo bars directly affect the lifespan and effectiveness of concrete footings. Knowing potential mistakes during installation helps avoid weak structures and ensures compliance with building regulations. This guide explores key errors to avoid when placing reo bar in concrete footings, offering valuable knowledge for construction professionals and builders dedicated to creating strong structural foundations.
Understanding Reo Bars and Concrete Footings
Reinforcement bars, or reo bars, are used as the framework inside concrete footings. These steel bars create a strong internal structure that improves concrete’s natural ability to withstand compression by adding important strength when being pulled or stretched.
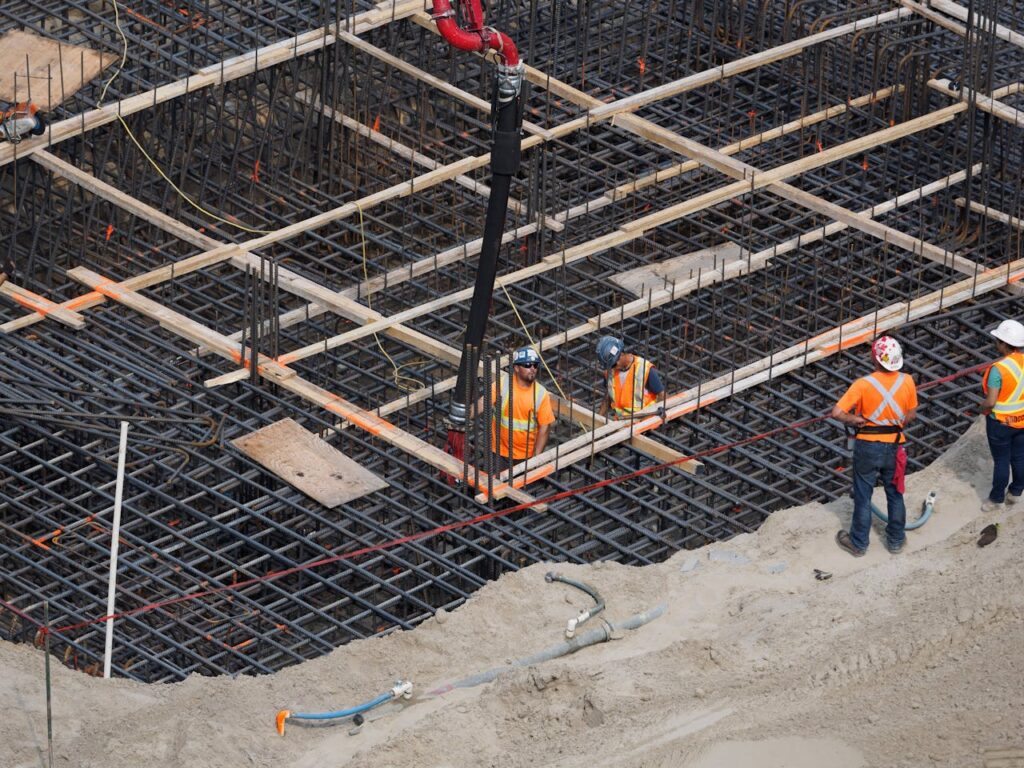
Common Types of Reo Bars:
- Standard carbon steel bars
- Epoxy-coated bars for corrosion resistance
- Galvanised steel bars for coastal applications
- High-yield strength bars for heavy-load structures
The selection of appropriate reo bar types depends on several factors:
- Environmental conditions
- Load requirements
- Soil characteristics
- Budget constraints
Critical Placement Specifications:
- Minimum Cover: 50mm from soil contact
- Bar Spacing: 200-300mm centre-to-centre
- Lap Length: 40x bar diameter for tension zones
- Support Height: 40-50mm above blinding layer
Proper rebar sizing directly affects how well footings perform. The diameter of reo bars can range from 10mm to 40mm, with 12mm and 16mm being standard choices for residential footings. If there are heavy structural loads, multiple layers of reinforcement may be needed.
Read more at: Choosing the Right Reobars for Residential and Commercial Slabs
When placing reo bars within concrete footings, it’s crucial to pay close attention to:
- Vertical and horizontal alignment
- Adequate concrete coverage
- Proper tie-wire securing
- Maintenance of designated spacing
Top 6 Mistakes to Avoid When Laying Reo Bar in Concrete Footings
Proper installation of reinforcement bars in concrete footings demands precision and attention to detail. These critical mistakes can compromise structural integrity and lead to costly repairs.
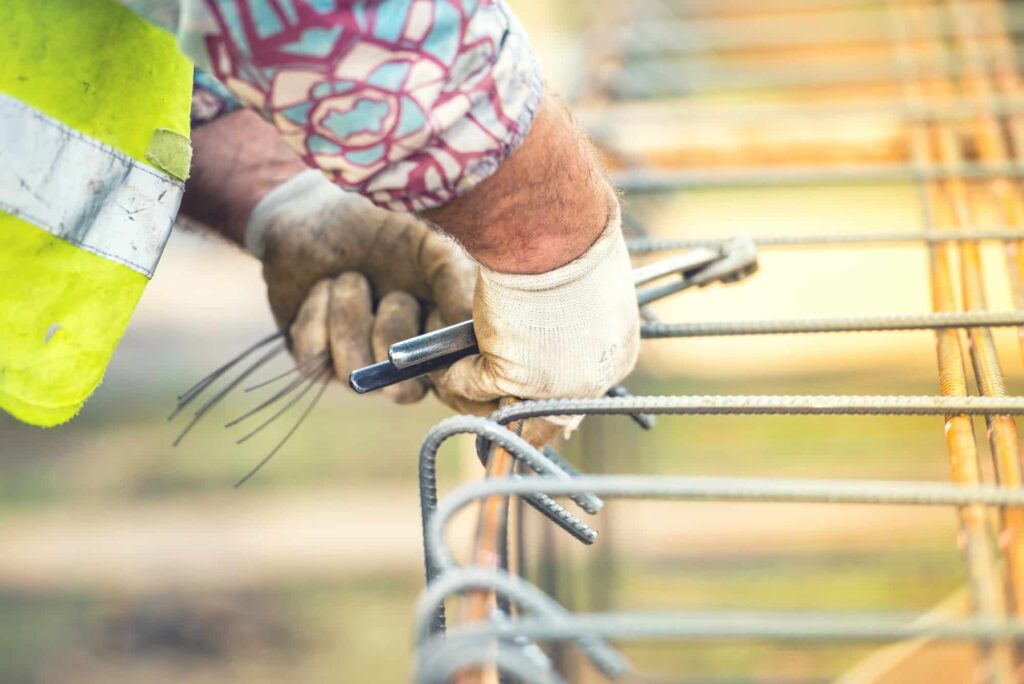
1. Inadequate Excavation for Footings
The foundation of successful reo bar installation begins with proper excavation. Incorrect trench dimensions create a cascade of structural issues that affect the entire building’s stability.
Common excavation errors include:
- Insufficient depth measurements
- Uneven trench bases
- Incorrect width calculations
- Poor soil compaction
Impact of improper excavation:
- Reduced load-bearing capacity
- Uneven settlement
- Structural cracking
- Foundation failure
A thorough soil analysis must precede any excavation work. Different soil types require specific approaches:
- Clay soils: Need deeper footings due to expansion properties
- Sandy soils: Require wider footings for load distribution
- Rocky terrain: Demands specialised excavation techniques
Engineering specifications dictate:
- Minimum footing depths
- Required soil bearing capacity
- Appropriate drainage provisions
- Reinforcement requirements
Professional soil testing reveals:
- Soil composition
- Load-bearing capacity
- Moisture content
- Potential ground movement
Best practices for excavation:
- Follow engineer-approved plans
- Document soil conditions
- Maintain consistent depths
- Ensure level trench bases
- Implement proper drainage systems
Accurate excavation creates the essential foundation for proper reo bar placement. Engineers specify minimum dimensions based on:
- Building loads
- Soil characteristics
- Local building codes
- Climate conditions
2. Improper Rebar Installation
Incorrect rebar installation poses significant risks to structural integrity and can lead to catastrophic foundation failures. The placement, spacing, and configuration of reinforcing bars demand precise attention to engineering specifications.
Critical Installation Errors:
- Insufficient concrete cover around rebar
- Incorrect lap splice lengths
- Improper bar spacing
- Missing or misplaced chairs and supports
- Wrong rebar size selection
The minimum concrete cover for rebar must meet Australian Standards AS 3600, typically ranging from 40mm to 75mm depending on exposure conditions. This protective layer shields the steel from corrosion and ensures proper load transfer.
Correct Positioning Guidelines:
- Use appropriate spacers and chairs to maintain rebar elevation
- Secure intersections with tie wire
- Maintain specified overlap lengths at splices
- Install corner bars at required angles
- Place additional reinforcement around openings
Neglecting proper rebar positioning compromises the footing’s ability to resist tensile forces. A concrete footing without correctly placed reinforcement can develop cracks under normal loading conditions, leading to structural instability and potential collapse.
The spacing between parallel bars must allow proper concrete flow during pouring. The minimum clear distance should be 1.5 times the maximum aggregate size or 40mm, whichever is greater. This spacing ensures adequate concrete consolidation around the reinforcement for optimal bond strength.
3. Using Poor Quality or Incorrect Concrete Mix
The quality and consistency of concrete mix directly impacts the structural integrity of concrete footings. A poorly mixed concrete batch can lead to severe durability issues and compromise the entire foundation system.
Critical Mix-Related Issues:
- Inconsistent Mixing: Uneven distribution of materials creates weak spots prone to cracking
- Incorrect Aggregate Ratios: Wrong proportions reduce concrete strength and workability
- Excess Water Content: Additional water weakens the concrete’s compressive strength
- Poor Quality Materials: Substandard cement or contaminated aggregates compromise durability
The water-to-cement ratio stands as a crucial factor in concrete strength. The ideal ratio typically ranges between 0.45 and 0.50. Higher ratios create a more fluid mix but significantly reduce strength and increase the risk of:
- Segregation during placement
- Excessive bleeding
- Reduced durability
- Surface scaling
- Internal void formation
Improperly mixed concrete leads to serious structural issues:
- Premature cracking
- Uneven settlement
- Reduced load-bearing capacity
- Surface defects
- Poor bonding with reo bars
The concrete mix must meet specific strength requirements based on engineering specifications. Regular testing of concrete samples helps ensure the mix maintains consistent quality throughout the pouring process. A properly designed mix provides optimal workability during placement while achieving the required strength for long-term structural performance.
4. Neglecting Proper Curing Procedures
Proper concrete curing is a critical phase in footing construction, requiring a minimum seven-day period for optimal strength development. The curing process allows cement particles to form strong bonds through hydration, creating a durable foundation for structural support.
Essential Curing Requirements:
- Maintain consistent moisture levels throughout the curing period
- Protect concrete from direct sunlight and wind exposure
- Keep concrete temperature between 10-21°C
- Apply curing compounds or wet hessian blankets for moisture retention
Rushing the curing process leads to significant structural weaknesses:
- Reduced compressive strength
- Increased surface cracking
- Poor durability against weather exposure
- Compromised load-bearing capacity
- Potential reinforcement corrosion
Effective Moisture Retention Methods:
- Water ponding on horizontal surfaces
- Sprinkler systems with controlled water flow
- Plastic sheeting secured tightly over concrete
- Specialised curing membranes
The relationship between curing time and concrete strength follows a direct correlation – proper curing can achieve up to 95% of the designed strength capacity. Inadequate curing might result in strength reductions of 30% or more, compromising the entire structural integrity of the footing.
Temperature Control Measures:
- Insulating blankets for cold weather protection
- Shade structures for hot weather conditions
- Regular temperature monitoring
- Adjusting water temperature during mixing
5. Ignoring Drainage Considerations Around Footings
Poor drainage around concrete footings creates severe structural vulnerabilities that can compromise the entire foundation system. Water accumulation near footings leads to:
- Soil erosion beneath the foundation
- Weakening of the supporting ground
- Potential settlement issues
- Concrete deterioration
Critical Drainage Solutions
The implementation of proper drainage systems requires careful planning and execution:
- Installation of aggregate layers
- 100mm minimum gravel bed beneath footings
- Crushed stone or clean gravel for optimal drainage
- Proper compaction to prevent settling
- Strategic placement of drainage pipes
- Perforated pipes positioned around footing perimeter
- Minimum 1% slope for effective water flow
- Connection to main drainage system
Prevention Measures
Protecting footings from water damage requires multiple defensive strategies:
- Waterproof membrane installation
- Proper ground grading (minimum 1:50 slope away from structure)
- Regular maintenance of drainage systems
- Installation of surface water diversion channels
Water accumulation near footings can cause soil expansion and contraction cycles, leading to structural movement and potential cracking. The cost of retrofitting drainage solutions post-construction significantly exceeds initial installation expenses. Proper drainage design must account for local soil conditions, rainfall patterns, and groundwater levels to ensure long-term foundation stability.
6. Skipping Inspections Throughout the Process
Regular inspections serve as critical checkpoints during concrete footing construction. Each stage requires thorough examination to maintain structural integrity and prevent costly repairs.
Key inspection stages include:
- Pre-pour inspection of excavation depths and dimensions
- Verification of soil conditions and bearing capacity
- Assessment of formwork alignment and stability
- Confirmation of reo bar placement, spacing, and tying
- Evaluation of concrete mix specifications
- Monitoring of pour techniques and consolidation methods
Qualified inspectors identify potential issues before they become permanent problems. A missing or incorrectly placed reo bar might go unnoticed without proper inspection, leading to structural weakness in the completed footing.
Common inspection oversights:
- Failing to check reo bar lap lengths
- Missing verification of concrete cover requirements
- Skipping reinforcement spacing measurements
- Neglecting to confirm proper tie wire installation
- Overlooking formwork bracing stability
Professional inspections document compliance with engineering specifications and building codes. These records protect builders and property owners by verifying that construction meets required standards.
Implementing a systematic inspection schedule creates accountability throughout the construction process. Each inspection builds upon previous checks, ensuring no critical elements are missed during the footing installation.
Best Practices for Formwork and Reo Bar Integration
Selecting appropriate formwork materials and implementing precise integration techniques creates the foundation for successful reo bar installation. The choice between F14 and F17 formwork plywood grades impacts both durability and concrete finish quality:
F17 Grade Benefits:
- Higher density composition
- Enhanced moisture resistance
- Superior load-bearing capacity
- Minimal surface imperfections
F14 Grade Applications:
- Cost-effective for temporary structures
- Suitable for non-critical areas
- Adequate strength for standard footings
- Acceptable finish quality
LVL (Laminated Veneer Lumber) formwork delivers substantial advantages in footing construction:
- 30-40% stronger than traditional timber
- Reduced material costs through multiple reuse cycles
- Precise dimensional stability
- Enhanced resistance to warping
Essential Alignment Tools:
- Digital laser levels
- String lines
- Adjustable spacers
- Steel measuring tapes
- Magnetic torpedo levels
Proper tool usage ensures reo bars maintain correct positioning within the formwork:
- Set spacing markers at regular intervals
- Check vertical alignment with plumb bobs
- Verify horizontal placement with laser levels
- Install bar chairs at specified heights
- Secure ties at intersection points
The integration of quality formwork materials with precise alignment techniques creates optimal conditions for concrete placement and curing. Regular calibration of measuring tools maintains accuracy throughout the installation process.
Additional Considerations for Coastal and Outdoor Projects
Coastal construction projects require specialised materials and protective measures to ensure the structure lasts. Rust-resistant reo bars are crucial in fighting against corrosion in areas with saltwater. These special bars have:
- A galvanised coating for extra strength
- Better resistance to chloride penetration
- A longer lifespan in marine conditions
- Less need for maintenance
The use of UV-resistant chain and shade mesh offers important protection during construction. These barriers provide several benefits:
- 90% UV protection for materials and equipment
- Prevention of concrete surface damage from direct sunlight
- Temperature control in work areas
- Dust containment during construction
Site mesh installation is important for both worker safety and environmental concerns:
- Noise reduction up to 40% in urban construction areas
- Prevention of debris scatter
- Enhanced site security
- Improved appearance for nearby properties
Combining rust-resistant reinforcement and protective mesh creates a strong system for coastal construction. Project managers should consider these factors in the early planning stages to make them most effective. The extra initial cost of these specialised materials leads to significant long-term savings through less maintenance and a longer-lasting structure.
Conclusion
Proper reo bar installation is essential for creating strong concrete footings and maintaining the overall stability of a structure. Every step of the construction process, from planning to inspections, plays a crucial role in building long-lasting reinforced structures.
Key takeaways for achieving optimal results:
- Strict adherence to engineering specifications
- Thorough site preparation and proper excavation
- Quality materials selection
- Precise rebar positioning and spacing
- Meticulous concrete mixing and placement
- Professional inspection at critical stages
These practices help prevent expensive repairs and potential structural failures. By investing in the right techniques, materials, and professional oversight, you can ensure better structural performance and lower maintenance needs in the long run.
To create exceptional reinforced concrete foundations, it’s important to understand common mistakes and follow industry best practices. This will result in strong, durable structures that can withstand time and reliably serve their purpose.